Design of a Flexible Gripper Structure for Fruit Picking
Professor Introduction
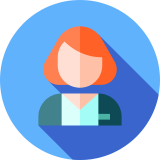
Gabriel | Ph.D. in Mechanical Engineering
Home Institute:South China University of Technology
[ Research Interests ] Design and optimization of flexible robotic grippers, microstructure modeling, and compression/impact mechanics; specific research areas include structural design and finite element simulation.
[ Additional Experience ] Extensive teaching and mentoring experience, known for being humble, responsible, approachable, and cheerful.
[ publications ] Published 29 SCI papers, with 16 as the first author or corresponding author, including 1 in the first quartile of the Chinese Academy of Sciences, 5 in the second quartile, and 8 in JCR Q1.
Project Description
The project focuses on the strategic development of rural revitalization and agricultural intelligence automation in China. It aims to design and optimize the mechanical properties of a flexible gripper for intelligent picking robots. The research includes: (1) Structural design of the flexible gripper using 3D modeling software (SolidWorks); (2) Topological optimization of the flexible gripper structure (Matlab); (3) Mechanical simulation of the gripper's motion (finite element simulation software Abaqus, ANSYS). The innovation of the project lies in the topological optimization of the gripper structure and the comparison and discussion of its gripping mechanical performance. The research outcome is an optimized flexible gripper for picking robots, which enhances the gripping performance of intelligent robots and contributes to the advancement of agricultural technology in China.
Project Keywords
Project Outline
Part 1 : Overview of Intelligent Picking Robots
• Importance and application prospects of intelligent picking robots
• Current design status and limitations of picking robot grippers
Part 2 : Research Objectives and Hypotheses
• Exploring the feasibility of flexible gripper structural design
• Optimizing the mechanical properties of flexible grippers to enhance gripping performance
Part 3 : Review of Existing Research and Methods
• Review of existing flexible gripper designs and their mechanical performance
• Existing topological optimization methods and their applications
Part 4: Structural Design of the Flexible Gripper
• 3D modeling using SolidWorks
• Designing a flexible gripper structure that meets picking requirements
Part 5 : Topological Optimization of the Flexible Gripper Structure
• Topological optimization using Matlab
• Optimizing material distribution and shape of the gripper structure
Part 6 : Mechanical Simulation of Gripper Motion
• Finite element simulation using Abaqus and ANSYS
• Evaluating the mechanical performance of the gripper under different gripping conditions
Part 7: Prototype Manufacturing and Experimental Validation
• Manufacturing the flexible gripper prototype
• Conducting practical gripping experiments to validate simulation results
Part 8: System Optimization and Parameter Adjustment
• Identifying and adjusting key parameters affecting gripping performance
• Optimizing gripper design based on experimental data
Part 9: Results and Discussion
• Graphical representation of experimental results and performance metrics
• Discussion of the significance and application prospects of the research results
• Comparison with existing gripper designs, analyzing advantages and limitations
Part 10: Conclusion and Future Research Directions
• Summary of key findings and their significance
• Identification of research limitations and suggestions for future research
• Recommendations for the application of flexible grippers in agriculture and other fields
Part 11: Reporting and Presentation
• Writing a detailed research report with clear structure, concise language, and accurate data presentation
• Preparing and delivering a clear and engaging oral presentation of research background, methods, results, and conclusions
Suitable for
High School Students:
• Interest in Robotics and AI : Students with a strong interest in mechanical engineering, robotics technology, and their applications.
• Basic Knowledge : Students with basic knowledge of physics and mathematics, and an understanding of computer-aided design tools.
University Students:
• Relevant Major : Students majoring in mechanical engineering, automation, robotics technology, or related fields.
• Software Skills : Familiarity with 3D modeling software (SolidWorks), programming languages (Matlab), and finite element simulation tools (Abaqus, ANSYS).